Planet
& Product
In defending the natural environment through its business practices, the F.I.L.A. Group is not merely complying with the law, but also applying one of its core values. We are committed to promoting sustainable policies designed to maintain and improve the quality and safety of our products.
The measures we adopt contribute to achieving the following Sustainable Development Goals:
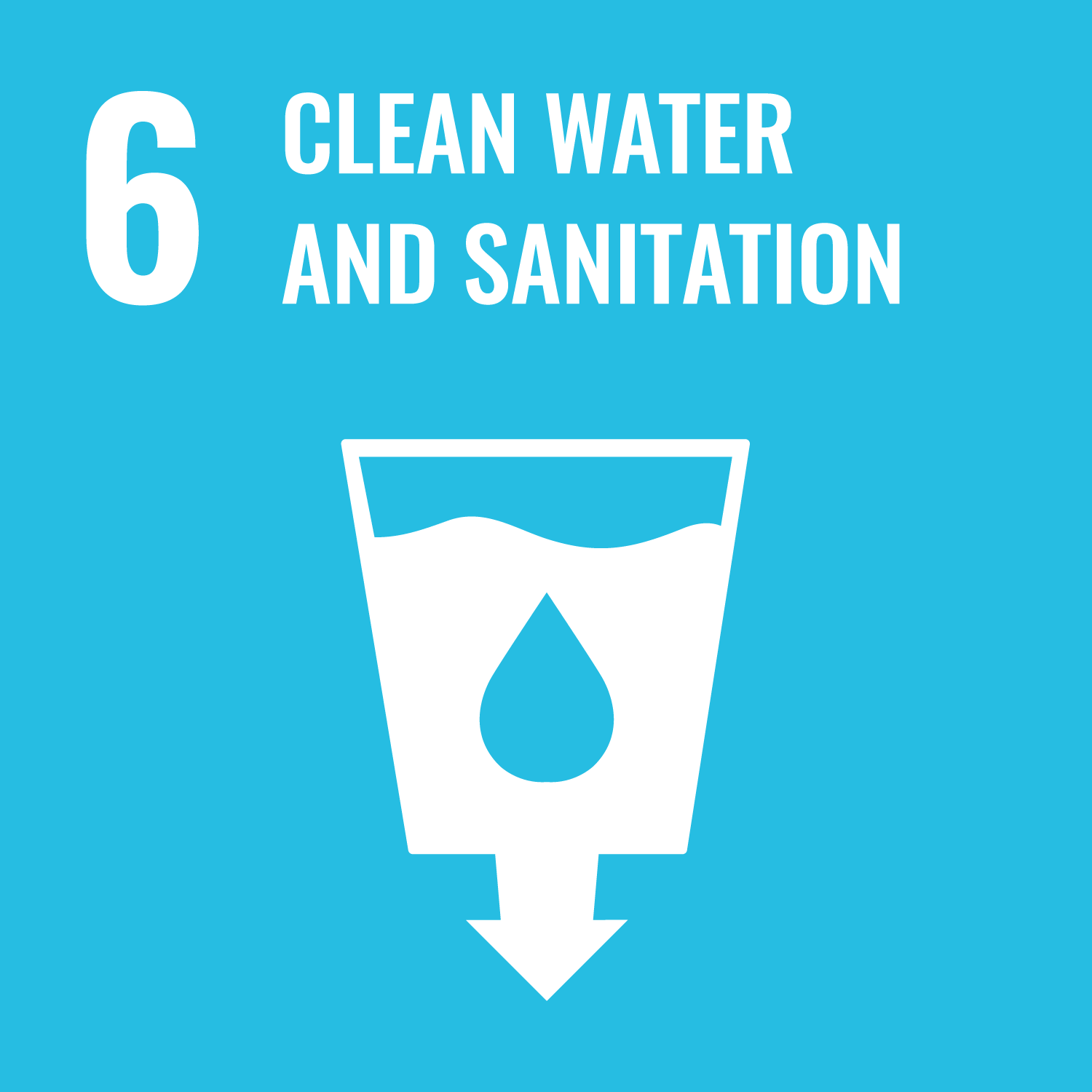
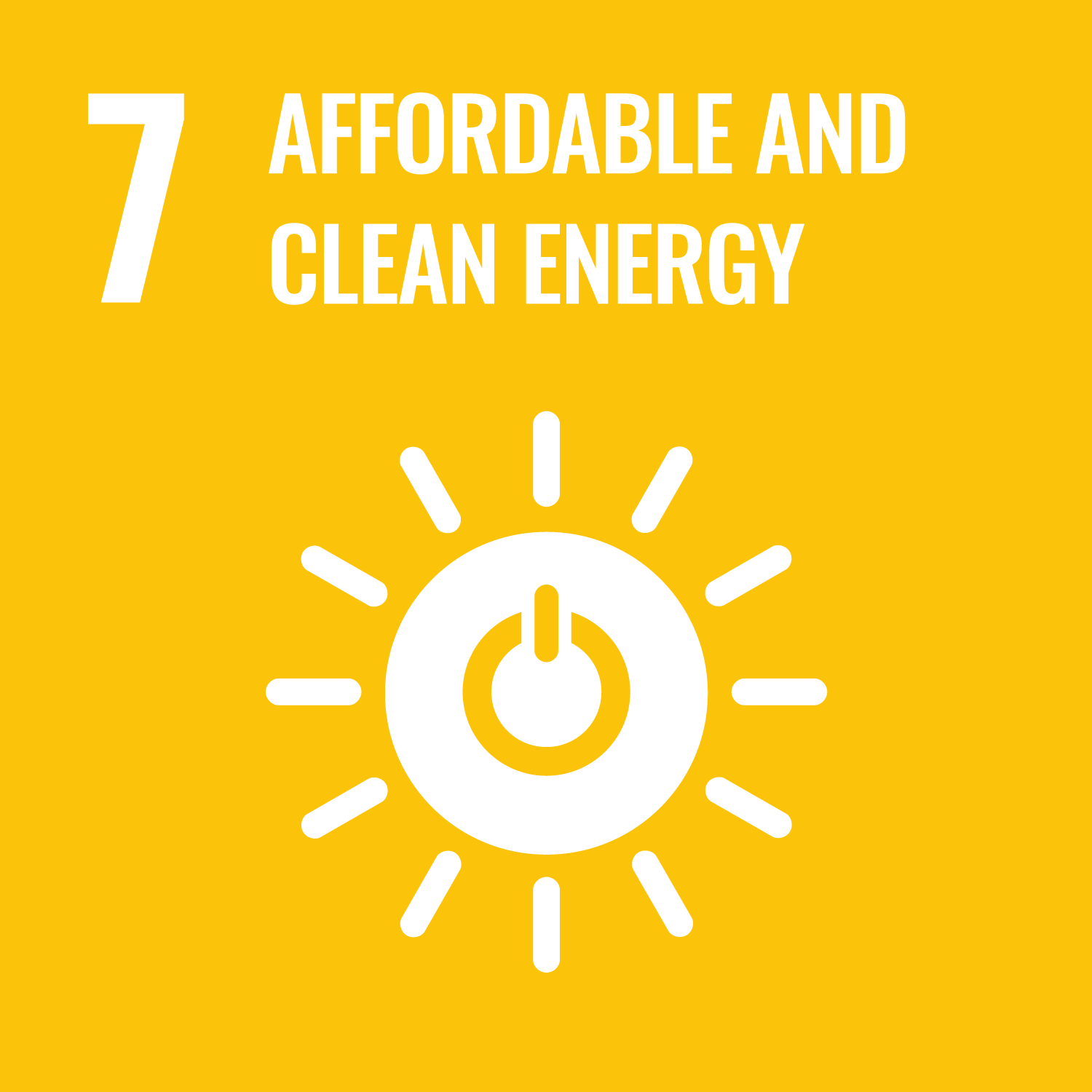
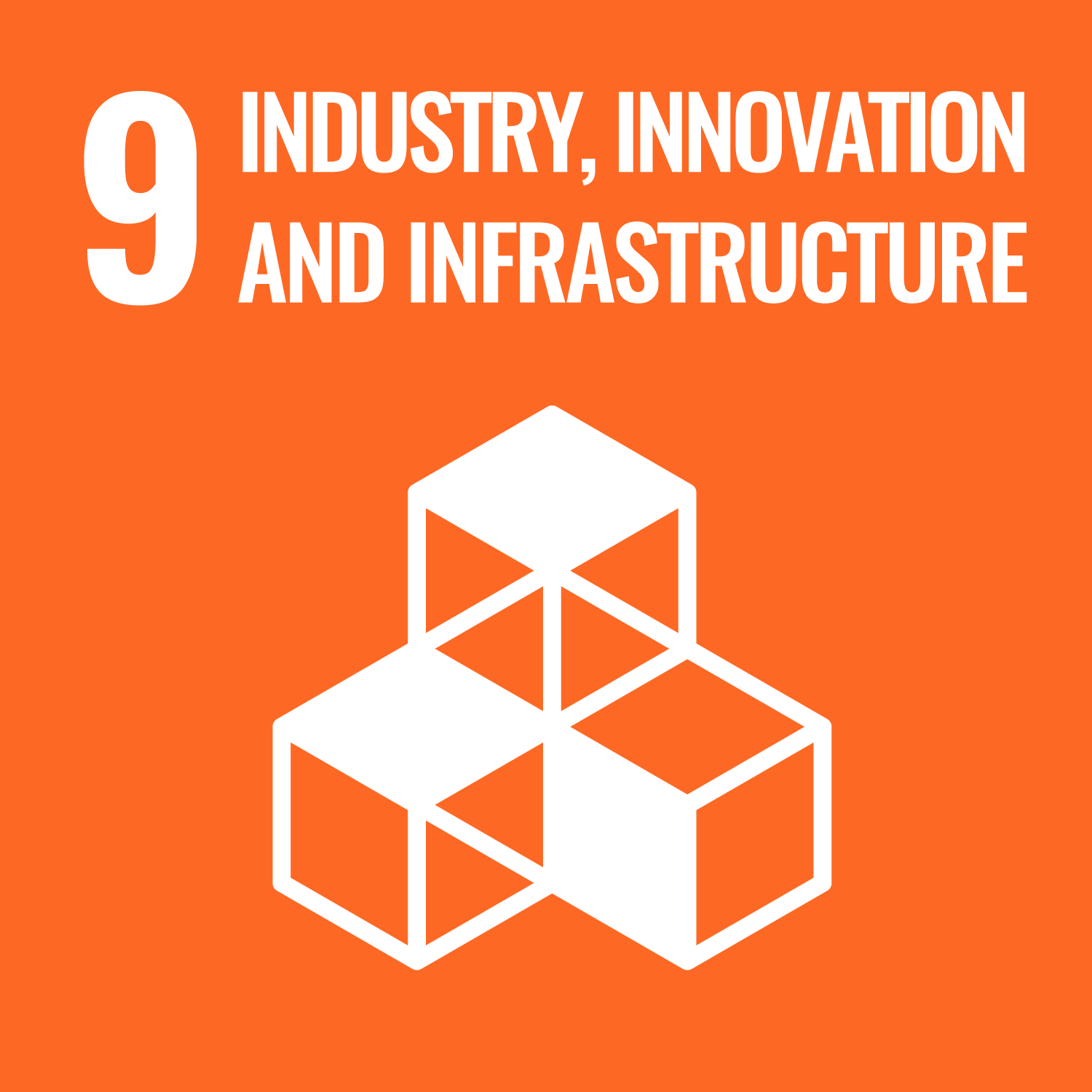
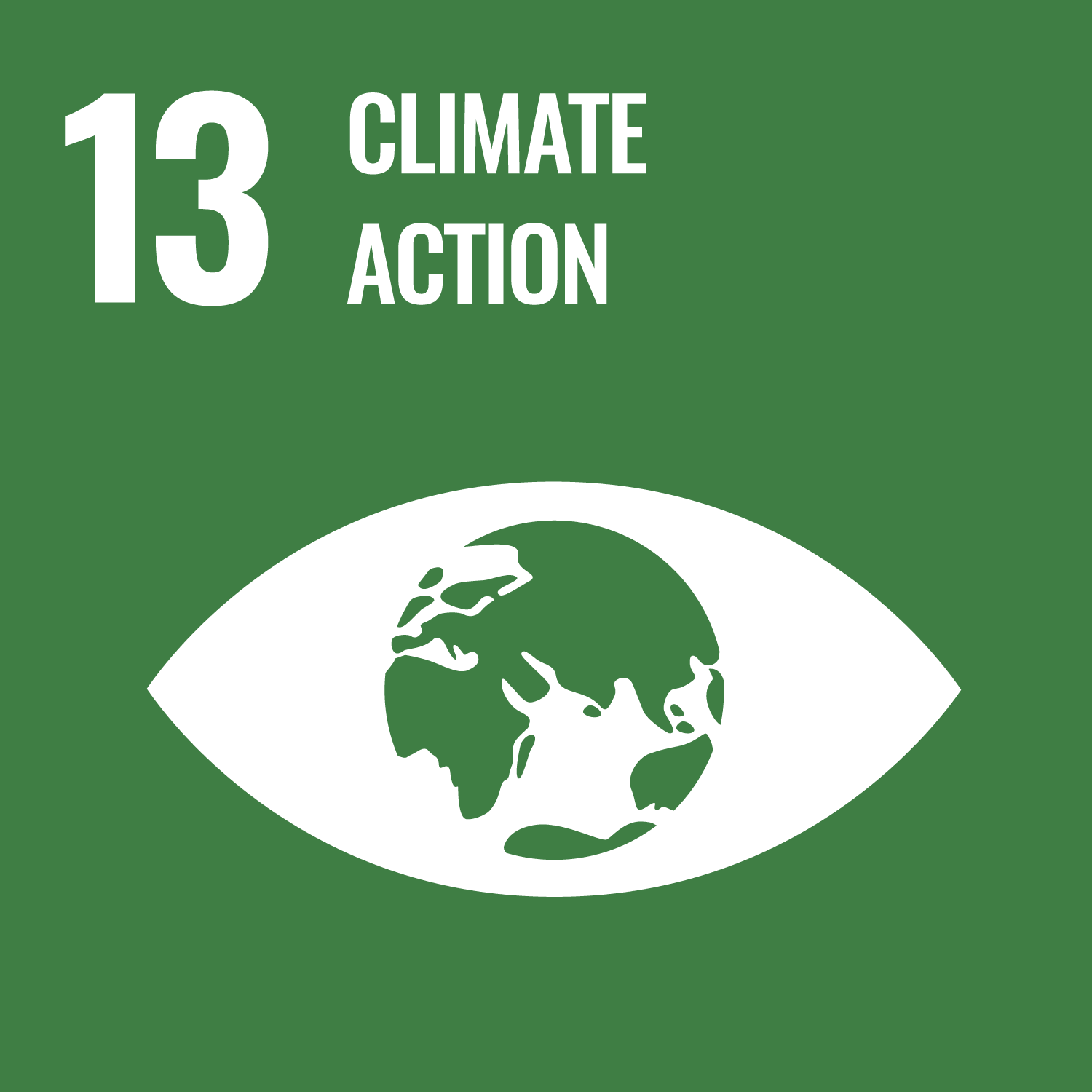
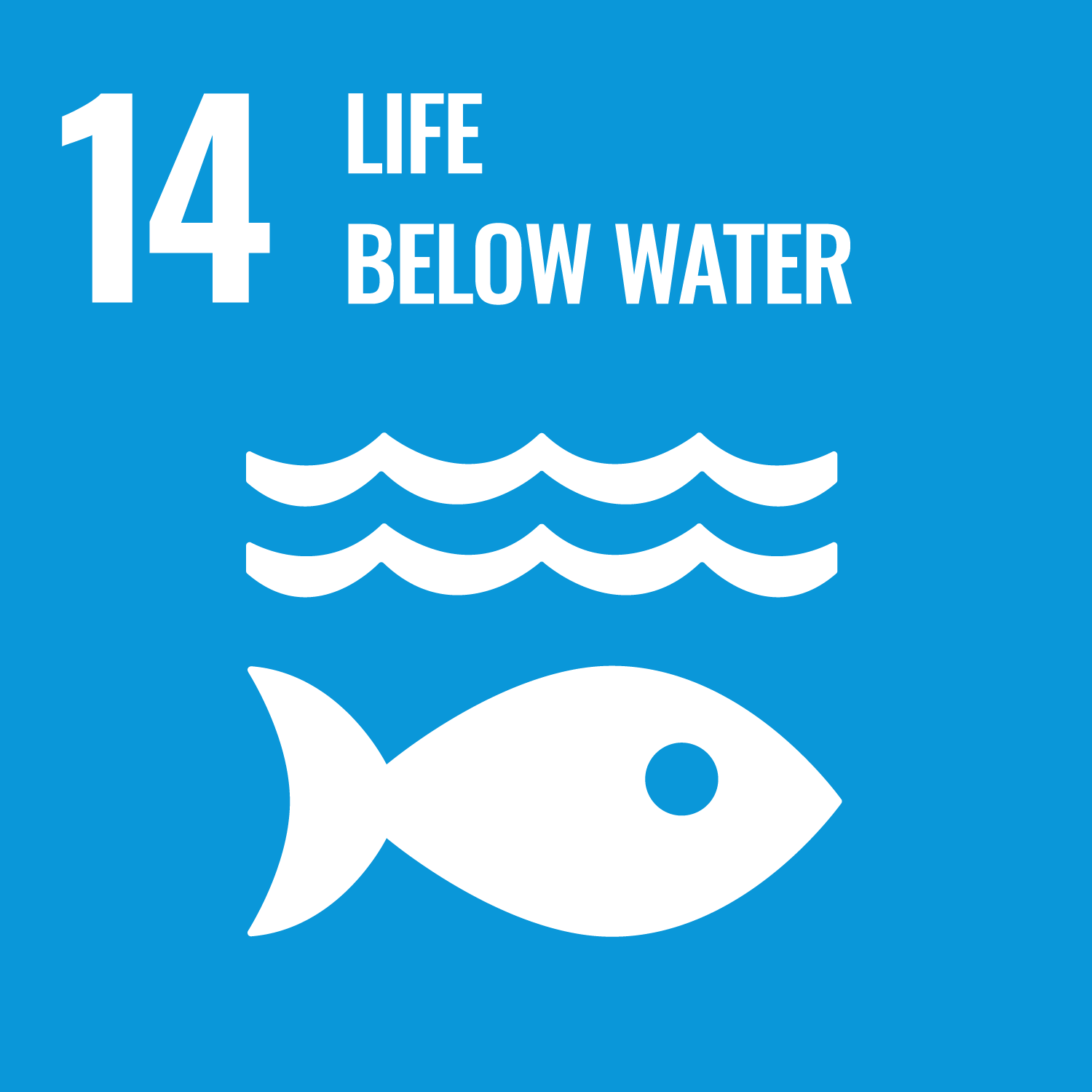
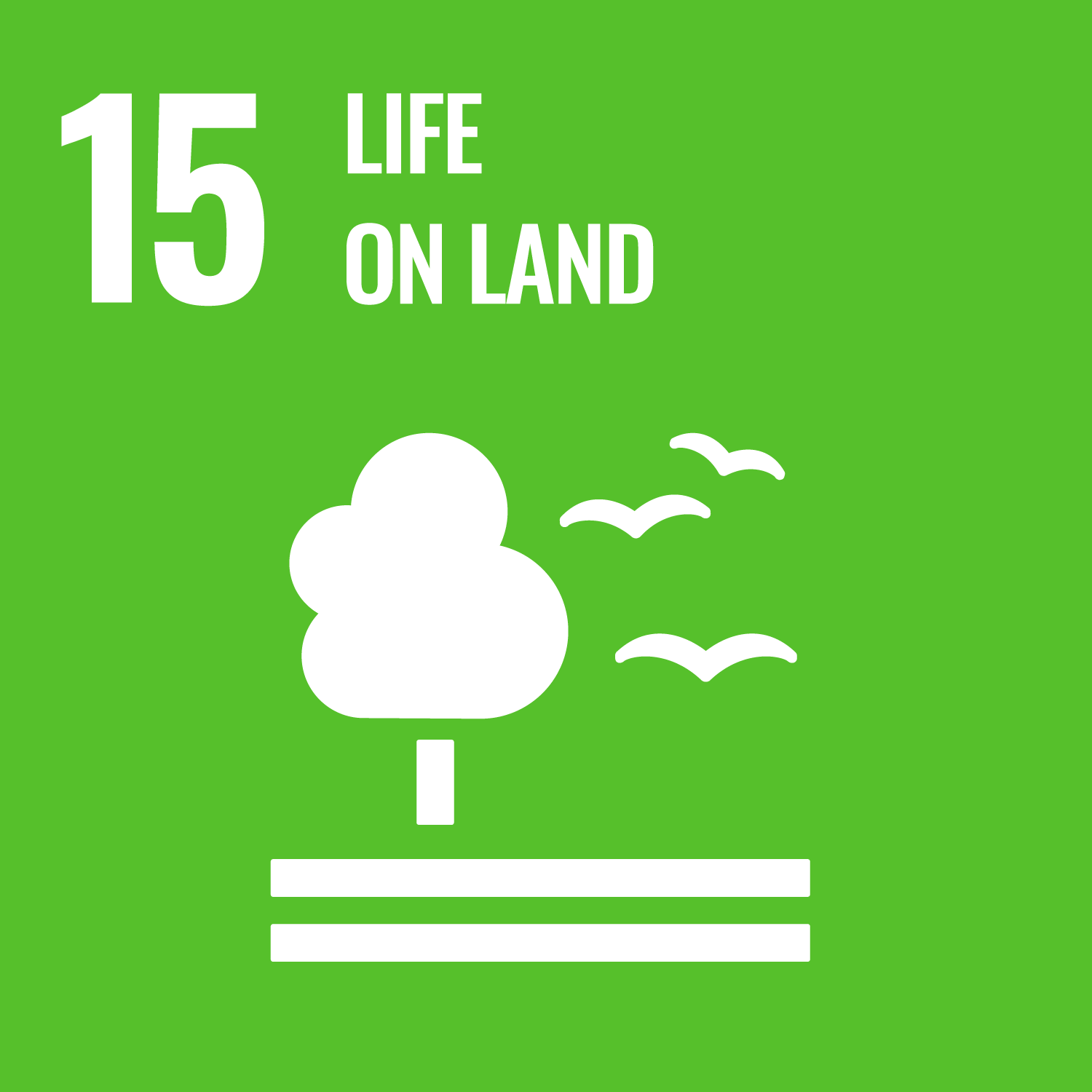
66%
of the Group’s waste is recycled and reused
98%
of the Group’s waste is non-hazardous
-15%
reduction in water withdrawals compared to 2022
10.246 CO2
Scope 1 emissions
20.152 CO2
Scope 2 emissions
101.801 CO2
Scope 3 emissions
Forests are facing a number of climate, environmental, man-made and socio-economic challenges. Forest conservation involves coordinated management between various operators.
Timber certification ensures the sustainable development of forests and allows us to ensure biodiversity, forest renewal, the prevention of natural disasters, the protection of key habitats and the reduction of the impact of forestry for future generations.
Timber and its by-products go through many steps before reaching you. The supply chain is long and complex and the information must be documented throughout the entire process, from the tree to the end product. Each link in the chain is therefore essential in ensuring full traceability through certification, which is why FILA has already introduced the use of timber and fibre sourced from responsibly, correctly and sustainably managed forests.
With PEFC (Programme for Endorsement of Forest Certification schemes) certification and FSC® (Forest Stewardship Council ®) certification we ensure that the timber used in our products meet the highest sustainable forest management standards.
Since the last century, one of the main woods used to manufacture our Lyra and Giotto pencils and coloured pencils is California incense-cedar, which apart from historically being one of the most suitable woods for pencil-making, has long satisfied strict sustainability protocols: Programme for Endorsement of Forest Certification schemes (PEFC). The cedarwood comes from the Californian forests, where new trees are planted as the mature trees are harvested, creating the next generation of forests. Harvesting cycles are at lengthy intervals and involve felling only a small percentage of the existing trees, according to clearly defined rules for maintaining biodiversity and promoting a natural mix of flora and fauna that allows the survival of animal species, including those that are endangered species.
In order to reduce waste, there is a working timber recovery system in place, a consolidated practice here at F.I.L.A. Group, in a move towards the adoption of a circular economy. This involves initiatives such as using tree bark and sawdust as fuel to generate heat (Oaxaca plant in Mexico), and making some of our ranges of pencil and frames for canvases from waste wood (Brideshore plant in the Dominican Republic). Across all the timber processing factories, sawdust and woodchip aspiration systems are present to capture sawdust and woodchips, which are then put to various uses.
At F.I.L.A., we have launched a plan to adopt ISO 14001:2015 environmental certification of our production plants, in order to identify and manage the environmental impact of our manufacturing activities and prove our commitment to environmental sustainability. In line with the requirements of the standard, each plant must: provide an environmental impact study, identify goals and plans to improve their performance and reduce external impact, implement the system involving all the stakeholders and perform reviews to ensure ongoing improvement of the Environmental Management System.
To date, the production plants that have received certification are the F.I.L.A. S.p.A. plants (Rufina plant and Pero offices), Canson France (plant in Grand Mourier, Moulin du Roy and Saint Germain La-Ville), Fila Arches, the Yixing plant and the Dixon Kunshan plant.
The world of plastics is continually evolving against a backdrop of growing sustainability. Over the last few years, research into innovative solutions in the field of bio-plastics has experienced significant growth. In our research and development departments, we study and test bio-plastics to understand their potential application for our products, their sustainability in the industrial process and the performance of the finished product. Bio-plastics contribute to the reduction of CO2 and are made from plant-based resources, which are therefore renewable, unlike fossil fuels.
To date, plant-based plastics have been found to be particularly valuable as a substitute for fossil-based plastics in some of our production processes. In 2019, we began introducing bio-plastic for the industrial production of durable and semi-durable items; starting with our glue and poster paint pots, and then our Didò eggs and most recently, the first bio-based LYRA Graduate ART-TIP pen. These eco-friendly products retain their product-preserving qualities and can be recycled as plastic after use (in case of packaging).
As of 2020, research into technical solutions with a view to circular economy – for the recovery of scrap materials and the reduction of waste – has experienced rapid growth. The result has been the introduction of regenerated plastics, in other words, plastics derived from salvaging industrial waste and by-products. These materials have replaced the fossil-based virgin raw materials used to produce all the barrels and caps of our Tratto1 and Tratto Matic ballpoint pens, our school packs and the pots used at school to hold felt-tips.
For the latter products, the challenge to identify a material that embodies the concept of circularity and, at the same time, complies with the EC Directive 2009/48/EC on toy safety (as regards both chemical and physical requirements), was a tough one. However, our efforts were richly repaid in the results we attained and has paved the way for new applications of regenerated materials and gradually increasing their use, compatibly with their suitability for our products.
Water is the principal natural resource used in paper production. Accordingly, the quality of the water supply is a priority for us. Canson® paper manufacturers use the pure waters of the Ardèche basin in France. The rivers around Canson® have been rated category 1 (classed as “excellent quality”) by the French water board, l’Agence de l’Eau.
For production, only water-based ink is now used for printing Canson® folders, drawing paper and graph paper. In addition, for glued pads, we use a neutral glue that, besides its environmental benefits, allows artwork to be kept in optimal condition.
During product design, we try to minimize waste generation at the source. Our efforts have been focused on reducing the percentage of wasted paper: by optimising our production and spool length, by reducing kerfs, by improving our equipment and making it function reliably, and through investments. Daler Rowney has invested in the most recent basket mill technology, allowing it to prepare pigment dispersion internally, in order to significantly reduce the amount of water consumed, but also energy consumption and emissions owing to transportation.
The raw materials for Canson paper for students and artists, like the Giotto paper produced at the Canson paper mill, use fibres from an FSC® certified chain and a biomaterial, starch, essential for increasing the paper’s resistance to ripping and tearing, for bonding the surface through sizing, and preventing the occurrence of dusting.
In F.I.L.A. Group’s production process, water is used for the paper mills (St. Cuthberts in Great Britain and Canson and Fila Arches in France), for the production of paints and glues (at the Canson plant in France, F.I.L.A. Dixon Group in Mexico, the Daler-Rowney facility in the UK, Maimeri in Italy, F.I.L.A. Yixing in China, Doms in India and at Canson Brazil), and for the production of play doughs (at the Rufina plant in Italy, Canson in Brazil and Dixon Group in Mexico).
All Group water withdrawals and discharges comply with the local legislative requirements and are checked regularly. Group Companies have adopted specific policies, investments and goals, confirming their commitment to reducing water consumption.
In 2017, at the Canson facility in Grande Mournier, France, a large rainwater decantation basin was built to separate any potential pollutants (such as hydrocarbons) before their controlled emission into the environment. Also at Canson France, at the Moulin du Roy facility, a water purification system (effluent plant) is used to treat water before introducing it back into the water course. A feasibility study has been launched into the reduction of water withdrawal.
The Chalon en Champagne production facility is home to a purification system for industrial waste waters resulting from the production processes. At the St Cuthbert’s paper mill, a new water treatment plant was built in 2019 to treat the water (effluent plant) before it is partially re-utilised for production and introduced back into the river.
The Dixon Mexico water purification plant in Oaxaca separates the water from the wax used in the production process. Whereas in China, at the Kunshan facility, steam is used during processing and discharged into systems located on the factory roofs, condensed and transformed into water for reuse in civil facilities.
For further examples, please refer to the Sustainability Report.
Durability and performance are two aspects that influence waste reduction: we follow this philosophy in everything we do, every single day. Our felt-tip pens last longer because the plastic components (bio-based, regenerated or fossil-based) are designed to prevent ink evaporation; we choose fibre tips, which are both soft and durable, retain their shape, and allow the ink contained in the reservoir to be used up completely. The felt-tip pens have brightly coloured inks and do not dry out even if the cap is left off for several days.
The pencils and coloured pencils are made with highly pigmented solid cores, which deliver instant colour to the paper, while wearing down slowly. The glue sticks do not disintegrate, are compact and deliver just the right amount of glue to the paper for optimum use; the poster paints are rich and concentrated and a small quantity offers excellent results. Lastly, the pens, highlighters and markers have a large ink reservoir and last for a long time.
In 2022, PONGO, the iconic Italian plasticine brand, produced in the Tuscan plant in Rufina, celebrated its seventieth year and became entirely sustainable by improving its performance. A plant-based formula, produced with ingredients of natural origin, selected from renewable sources. The new plasticine is always soft, with bright and vivid colours, never dries out, is easy to mould and does not stain hands or surfaces.
A watchful
eye on packaging
The choice of materials used for packaging is another crucial aspect for the growth of the Group with an eye to a sustainable future. That is why our goal is to gradually reduce packaging to the bare minimum, compacting it to minimise waste and emissions. We seek out environmentally-friendly solutions for our packaging, promoting the use of card, preferably recycled. We are gradually reducing plastic packaging to ensure the product remains undamaged in transport and at the point of sale. We now use exclusively single-component packaging that is easy to recycle.
Furthermore, we are progressively replacing fossil-fuel plastics with alternative materials such as recycled R-PET plastic for envelopes and blister packs.
Two recent examples are:
lasticine packaging, including the new Pongo, where we implemented only essential packaging in order to store and preserve the product and guarantee its quality during use. We use exclusively single-component packaging that is easy to recycle. By streamlining the packaging of the plasticine range, we now avoid using and transporting 4.7* tons of cardboard every year. (* This estimate was obtained from volumes placed on the market in 2021)
Two recent examples are:
We have completely eliminated the internal plastic tray from around 300,000 packs of Giotto Decor felt-tip pens, thus reducing the size of the pack and the use of cardboard.
The F.I.L.A. Group quality control process, managed by the Quality Assurance department, consists of two phases: static control and process control.
“Static control” involves various tests conducted in the Group’s internal laboratories, also used to test products in the research and development phase, whereas “process control” involves various tests carried out on an ongoing and/or scheduled basis throughout the stages of the production process by production staff and Quality Assurance. Such tests are performed in addition to the technical tests required by national and international standards and/or customer specifications.
In addition to internal tests to verify product safety, F.I.L.A. Group also uses external laboratories, primarily accredited ones, to obtain third-party safety standard compliance certificates. Each of the Group’s production sites liaises and maintains an ongoing relationship with its own historical reference institute, whereas subsidiaries outside the European Union obtain certificates issued by globally accredited institutes.
The management of product safety takes the product category into account, i.e. products classified as toys, products classified as “cosmetic toys” and products classified neither as toys nor as cosmetics.
In our research and development departments, we study and test bio-plastics to understand whether they are suitable for our products, sustainability in the industrial process and performance of the finished product.
Discover our sustainability policies